What is a wet-laid nonwoven fabric? The wet-laid nonwoven fabrics: The fiber raw materials placed in an aqueous medium are opened into single fibers, and at the same time, different fiber raw materials are mixed to form a fiber suspension slurry, and the suspension slurry is transported to a network forming mechanism. Fibers are laid in the wet state and consolidated into cloth.
One of the main spinning methods of chemical fiber(
wet-laid non woven manufacturer), referred to as wet spinning. Wet spinning includes the following steps: (1) preparing the spinning dope; (2) extruding the dope from the orifice to form a fine stream; (3) solidifying the raw liquid into a primary fiber; (4) winding the primary fiber or directly post-processing.
The fiber-forming polymer is dissolved in an appropriate solvent to obtain a solution having a certain composition, a certain viscosity, and a good spinnability, which is called spinning dope. Spinning dope can also be directly obtained from homogeneous solution polymerization. The polymer swells before it dissolves, that is, the solvent first penetrates into the polymer, increasing the distance between macromolecules, and then dissolves to form a uniform solution. The entire process takes a long time, and the speed of the swelling process has a significant effect on the rate of dissolution. Prior to spinning, the polymer solution must be subjected to a pre-spinning process such as mixing, filtration and defoaming so that the spinning dope is uniform in its properties, and the entrained gel pieces and impurities are removed and the bubbles in the solution are removed. . In the production of viscose fibers, preparation before spinning also includes a ripening process to make the viscose with the necessary spinnability.
The spinning dope(
wet-laid non woven on sales) is sent to the spinning machine by a circulating pipe, metered by a metering pump, and then passed through a candle-shaped filter and a connecting pipe to enter the spinneret (cap). The spinneret is generally made of an alloy of gold and platinum or a niobium alloy material. A number of holes are regularly distributed on the spinneret, with an aperture of 0.05-0.08 mm. The trickle of the raw liquid pressed out from the nozzle hole enters the coagulation bath, the solvent in the stream of the raw liquid diffuses into the coagulation bath, and the coagulant penetrates into the stream, so that the stream of the raw liquid reaches a critical concentration and precipitates in the coagulation bath to form a fiber . The diffusion and solidification in wet spinning are physical and chemical processes, but some chemical fibers also undergo chemical changes simultaneously during wet spinning. For example, viscose fibers decompose cellulose naphthalate into cellulose regenerated fibers.
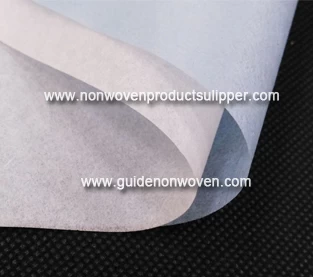
The wet spinning speed (referring to the first godet speed at which the primary fiber is taken up) is limited by the double diffusion rate of the solvent and coagulant and the fluid resistance of the coagulation bath, and is therefore much lower than the melt spinning speed. The ratio of the linear speed of the first godet to the extrusion speed of the spinning dope is referred to as the spinneret draw ratio. Wet spinning draw ratio is generally negative, zero, or very small positive value, the purpose is to improve the stability of the forming process.
The spinning dope is a viscous and elastic elastomer. When the undiluted liquid is pressed out from the spinning hole, there is an aperture swelling effect (Barras effect), so that the diameter of the extruded fine stream is larger than the diameter of the spinning hole. In the wet spinning process, the expansion ratio is generally 1 to 2.
Under the action of the tensile force of the first godet, the extruding fine stream tapers after passing the maximum diameter, and the refining process continues until the raw liquid stream is completely solidified. The change in the diameter of the thin stream in the wet spinning is not only the result of the stretching deformation but also related to the mass transfer process. The spinning process from the spinneret to the solidification point is the fiber forming zone, which is the key area for the formation of the fiber structure.
Wet spinning primary fibers(
wet-laid non woven vendor) are in a swollen state because they contain a lot of liquid. Macromolecules have a great deal of activity, and the degree of orientation is very low. Their morphological structure is closely related to the spinning process conditions. By selecting and controlling spinning process conditions, fibers of different cross-sectional shapes or special capillary pore structures and special properties can be produced. Wet spinning has a variety of different forming methods, spinning machine also has a variety of different structures. For example, there are single-bath or double-bath methods, deep-bath or shallow-bath methods, funnel forming or tube forming.
Wet-filament spinning machines are available in centrifuge or tube-type. Spinning a post-processing machine is usually used for spinning the short fibers, and the primary fibers formed at the respective spinning sites are bundled and continuously processed.
Wet spinning requires not only a wide range of bulk liquid preparations and pre-spinning equipment, but also coagulation baths, recycling and recycling equipment. The process flow is complicated, the plant construction and equipment investment costs are high, and the spinning speed is low. Higher. Tens of thousands of holes in the spinneret can be used in the production of staple fiber or a spin packer to increase production capacity. In general, only synthetic fibers that cannot be melt-spun, such as polyacrylonitrile fibers and polyvinyl alcohol fibers, are suitable for wet spinning a polymer solution to produce staple fibers and filament bundles.